— Сергей, складывается ощущение, что предприятия добывающего и перерабатывающего производства, еще недавно бывшие «на ручном управлении», стремительно цифровизируются. Это верное наблюдение?
— Не совсем. По крайней мере, в нашем случае. Для того чтобы начать создавать цифровое предприятие, необходимо заложить базис: станки с ЧПУ, АСУ ТП, системы управления производством, ERP, MES, системы аналитики. Автоматизация в промышленности идет уже давно. По моим ощущениям, массово отрасль занялась этим около 10 лет назад. К примеру, мы 10 лет назад начали внедрять на своих предприятиях систему SAP, переходили на нее постепенно, и сейчас у нас одна из самых развитых SAP-практик в Восточной Европе. И это в том числе стало фундаментом, который сейчас позволяет нам реализовывать «цифровые» проекты.
Если предприятие полностью индустриальное, с технологиями 1950–1960-х гг., никакого резкого перехода в «цифру» не будет. Отличие автоматизации от цифровой трансформации в данном аспекте состоит в том, что последняя вызывает ажиотаж: есть интерес со стороны СМИ и государства, сами компании регулярно сообщают о своих успехах. К автоматизации такого интереса не было, поэтому она прошла менее замеченной. И возможно, из-за этого складывается такое обманчивое впечатление о резком переходе предприятий из индустриальных в цифровые.
Нюанс в том, что очень сложно провести грань между автоматизацией и цифровизацией. На профильных конференциях под брендом цифровой трансформации часто представляют задачи автоматизации, которые мы решили лет 5–7 назад. Единое понимание того, когда именно предприятие становится цифровым, — большая область для дискуссий. Можно ли считать внедрение видео-конференц-связи цифровой трансформацией? А разработку мобильных систем ТОИР (техническое обслуживание и ремонт)? А внедрение интернет-магазина, осуществляющего продажу нашей продукции? К сожалению, единого отраслевого индекса цифровизации предприятия пока не существует.
При этом я не исключаю, что многие предприятия нашей отрасли уже цифровые, по крайней мере частично.
— Термин «Индустрия 4.0» славится большим количеством трактовок. Как вы определяете его для себя?
— Для нас Индустрия 4.0 — это новый взгляд на наше производство, который обеспечивают современные ИТ. В первую очередь я имею в виду новые технологии анализа данных и построения оптимизационных моделей с применением методов машинного обучения и искусственного интеллекта. Значительная часть активностей по digital-трансформации компании тесно связана с накоплением и обработкой данных. Когда они правильно собраны и структурированы, с помощью специальных алгоритмов машинного обучения можно выявлять зависимости, которые не способен заметить человек. Как следствие, можно настроить процесс автоматического принятия решений, что позволяет исключить участие человека и достигнуть нового уровня автоматизации производства.
Мы также активно инвестируем в технологии дополненной и виртуальной реальности. На прошедшей в ноябре 2018 г. выставке «Металл-Экспо 2018» мы представляли решения в области виртуальной реальности, которые вызвали немалый интерес у участников. Где применяются данные технологии? Для демонстрации возможностей нашей продукции, проведения тренингов, создания интерактивных инструкций, доступных непосредственно на месте проведения работ. И конечно же, это начало пути, по которому мы будем двигаться в направлении «цифрового двойника» производства.
— Сколько времени понадобится, чтобы все ваши предприятия перешли на работу с «цифровыми двойниками»?
— Цифровая трансформация предприятий нашего масштаба — задача далеко не одного дня и даже не одного года. Отдельные решения уже работают прямо сейчас — например, на нашем складе горячекатаных рулонов ЧерМК. Но переход от лабораторных испытаний и единичных моделей к массовому внедрению — очень амбициозная задача.
Главные бенчмарки цифровой трансформации — это в первую очередь модели и алгоритмы, которые помогают делать выводы на основании больших данных. Это, безусловно, «цифровые двойники», модели для предиктивного технического обслуживания, рекомендательные системы.
— Когда в вашей компании было создано подразделение инноваций? Каковы его задачи и долгосрочные цели?
— Инновационным развитием ИТ «Северстали» и трансформацией компании в этом направлении занимаются четыре подразделения: офис трансформации, «Северсталь-инфоком», «Северсталь диджитал» и бизнес-система «Северстали». Такой подход дает положительные результаты, главный из них в том, что итоговое решение является максимально эффективным, поскольку одну и ту же проблематику исследуют команды различного профиля с разных сторон.
Наше управление в «Северсталь-инфоком» было создано в августе 2017 г. Его главными задачами были поиск, быстрая проверка и «адаптация» в компании новых ИТ-решений и ИТ‑процессов. Например, в «Северстали» знали, что с помощью компьютерного зрения на производстве можно определять дефекты в готовой продукции и контролировать ход технологического процесса. Но компания не обладала тиражируемой экспертизой по этому направлению. Как реализуются подобные проекты? Cколько они стоят? Эти вопросы были актуальными еще чуть более года назад. За время своей работы мы реализовали около 10 кейсов только по этому направлению, что-то «взлетело», что-то нет, но самое главное — теперь мы точно знаем, что такое компьютерное зрение, как его использовать, какие есть ограничения, какие задачи и в какой срок можно решить с его помощью.
Или, например, проекты с виртуальной реальностью, с помощью которой мы разработали тренинг для сталеплавов по замеру температуры плавки и снятию пробы конвертерной стали, который позволяет проводить обучение и принимать экзамены в виртуальном электросталеплавильном цехе. Также мы создали прототип решения по позиционированию персонала, которое определяет, где находятся работники — в динамической или статической опасной зоне, и сигнализирует работнику и диспетчеру об этом. Важным направлением также является разработка чат-ботов для клиентов, которые уже сейчас за счет применения распознавания естественного языка во многом способны заменить классические call-центры.
Очень важное направление для нас — обучение новым технологиям. Не так давно было много шумихи вокруг блокчейна, и нам регулярно предлагали разработать решение на его основе. Мы организовали обучение, которое прошли около полутора тысяч работников компании, после чего произошел качественный сдвиг в предлагаемых идеях.
Очень сложно провести грань между автоматизацией и цифровизацией. На профильных конференциях под брендом цифровой трансформации часто представляют задачи автоматизации, которые мы решили лет 5–7 назад. Единое понимание того, когда именно предприятие становится цифровым, — большая область для дискуссий.
— Как вы искали решения по обозначенным направлениям?
— Поиск решений — это всегда творческий процесс, основанный на сочетании опыта команды, предложений на рынке, идей стартапов, результатов референс-визитов, посещения конференций и изучения успешного опыта цифровизации наших коллег и конкурентов.
Дополнительно мы проводим достаточно большую работу со стартапами. Мы собираем их на питч-сессии, предлагаем реализацию совместных прототипов, и те, кто нам подходит, могут рассчитывать на финансирование.
— Расскажите о наиболее значимых пилотах и проектах в области предиктивной аналитики состояния оборудования и Big Data.
— Данным направлением в нашей компании занимается подразделение CDO. Большинство текущих проектов «Северстали» в рамках процесса цифровизации можно разделить на два направления: предиктивные ремонты и управление качеством. Например, сейчас на Череповецком металлургическом комбинате в промышленной эксплуатации находятся две предиктивные модели, позволяющие предсказывать поломки на стане горячей прокатки. За 8 месяцев эксплуатации удалось предотвратить около 10 аварийных ситуаций, и только на сокращении простоев ожидается годовая экономия в 200 млн рублей.
В рамках управления качеством компания работает над моделями, которые смогли бы предсказать, удовлетворяем мы заявленным параметрам заказа клиента или нет, на разных этапах производства. Сейчас в эксплуатацию запущено несколько моделей, и компания работает над увеличением их числа. Компания видит в этом большой потенциал с точки зрения как улучшения качества продукции, так и экономического эффекта.
Оборудование на наших промышленных площадках оснащено десятками тысяч датчиков, поэтому для хранения и обработки поступающей с них информации мы создали крупнейшее среди промышленных компаний России гибридное хранилище данных — Data Lake. Его емкость составляет 2 петабайта, и, по нашим прогнозам, оно должно заполниться в течение 5 лет. И это с учетом того, что у нас еще есть неоцифрованные производственные цепочки, которые мы планируем цифровизировать.
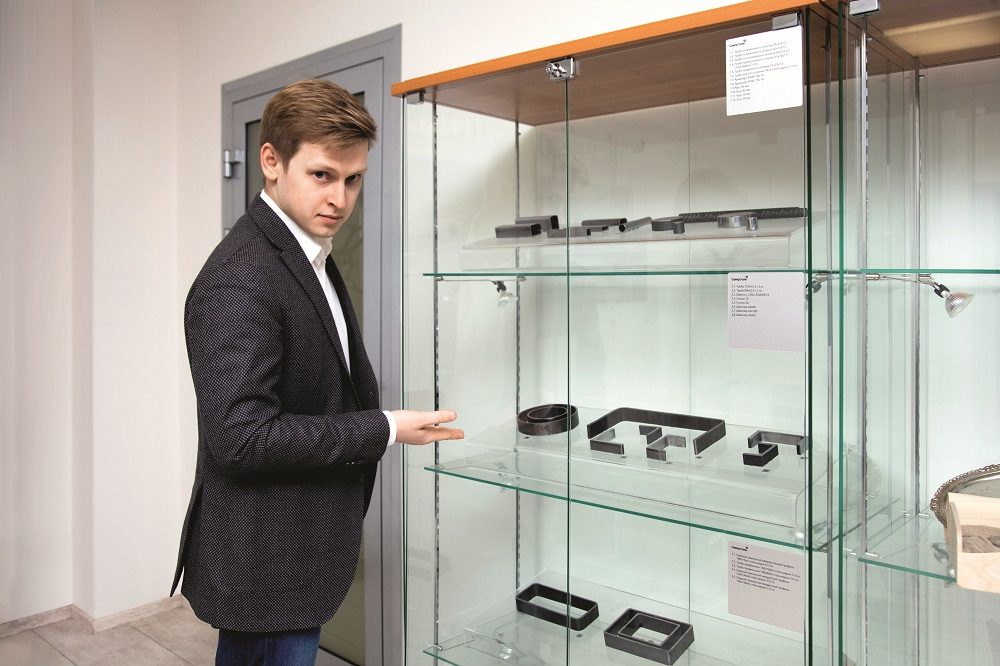
1.3 млн.
единиц оборудования в машиностроении
будет подключено к промышленному интернету к 2019 г. в России
— В ваш холдинг входят десятки предприятий. Интегрированы ли они между собой с точки зрения ИТ?
— Да, конечно. У нас единая SAP-система, работающая для всего ресурсного дивизиона и дивизиона «Российская сталь». С точки зрения ИТ у нас три основные площадки: Воронеж, Москва и Череповец. В Череповце находится наш ЦОД, где работают все производственные системы.
— Был ли у вас негативный опыт на тех или иных этапах цифровой трансформации?
— Скорее всего, этот опыт еще впереди. Если мы говорим о цифровой трансформации, она началась в 2017 г., и нам еще только предстоит пройти этот путь. Сейчас мы формируем видение того, как сделать наше предприятие цифровым. В процессе его реализации наверняка появится и негативный опыт.
— Тогда в каких областях вы ожидаете подвоха?
— Данные, конечно. Сбор, интерпретация, недостаточный эффект — всё это может стать проблемой.
— Как вы оцениваете ИБ-риски в связи с появлением умных устройств в корпоративной сети?
— У нас высококлассное управление информационной безопасности, которое участвует в обсуждении каждого пилотного проекта по внедрению новых технологий. В нашем случае они полноправные участники процесса цифровой трансформации, которые помогают принять правильное решение. Наша компания в целом очень ответственно относится к вопросам безопасности — как производственной, так и информационной, поэтому относительно ИБ-вопросов я спокоен.
— Как и где вы ищете специалистов по IIoT, Data Science, Machine Learning?
— ИТ-подразделения «Северстали» есть везде, где находится наше производство. Это более 10 городов, при этом три самых крупных центра я уже называл: Москва, Воронеж и Череповец. Мы активно нанимаем людей по всей стране, хотя дефицит специалистов все равно есть, иногда бывает сложно закрыть даже относительно простые вакансии.
Мы ищем специалистов повсюду: на рынке, внутри компании и в вузах. У многих «цифровых» специализаций не такой высокий порог входа, как принято считать. Если вы хороший разработчик с высоким уровнем технических навыков, то переход в тему Machine Learning, компьютерного зрения или распознавания естественного языка займет у вас 2–3 месяца.
Кстати, для привлечения новых кадров мы регулярно выступаем в вузах, где рассказываем о «Северстали», о том, какие инновационные и интересные задачи у нас есть. Многим наша компания представляется негибкой и никак не связанной с цифровизацией, хотя это не так. Показательно, что те, кто приходит на собеседования, зачастую поражаются проектам, которые мы реализуем.
— А есть ли в «Северстали» новые луддиты?
— Скорее, существуют вполне понятные опасения насчет нововведений, которые присущи любому человеку. Каждый работник хочет защитить себя и свои уникальные знания. Но ведь новые технологии — это не угрозы, а возможности. И зачастую даже самые современные технологии не могут заменить опыт людей, которые уже 10–15 лет трудятся на производстве. Для реализации цифровых проектов нам необходимы эти знания, без опыта наших работников и их инсайтов цифровизировать конкретный участок производства попросту невозможно.
— Обмениваетесь ли вы опытом внедрения инновационных решений с коллегами?
— Да, это могут быть референс-визиты, внутриотраслевые закрытые мероприятия, посещения профильных конференций и выставок. Мы очень любим общаться с коллегами, со специалистами из смежных отраслей — из таких компаний, как «Газпром нефть», «СИБУР Холдинг», Сбербанк.
Зачастую даже самые современные технологии не могут заменить опыт людей, которые уже 10–15 лет трудятся на производстве.
— Поделитесь своим видением перспектив Индустрии 4.0 в целом для российской экономики.
— С точки зрения перспектив для страны цифровизация — это обязательный фактор конкурентоспособности. Причем руководство страны это отлично понимает, судя по программе «Цифровая экономика», принятой летом прошлого года. Индустрия 4.0 как одно из ее ключевых направлений способна создать новые рабочие места, вывести на новый уровень производство товаров и услуг и повысить конкуренцию на мировом рынке.
Все больше промышленных компаний будут переходить к цифровому производству. Нужно быть готовыми к тому, что и клиенты, и поставщики станут «цифровыми» компаниями, поэтому необходимо активно интегрироваться в эти процессы и внедрять новые технологии. По оценкам экспертов, к 2019 г. в России к промышленному Интернету вещей будет подключено 1,3 млн единиц оборудования в машиностроении и 600 тыс. — в процессном производстве. А объем рынка промышленного искусственного интеллекта к 2021 г. составит $380 млн.
Также в ближайшие годы очень важными станут межотраслевые проекты — решения по экологии или охране труда, которые значимы для всех компаний. Это могут быть решения в области искусственного интеллекта, которые сейчас чересчур дороги для одной компании, но при этом могут обеспечить позитивное развитие для всего рынка.